Mama Mia BTS
December 9, 2022
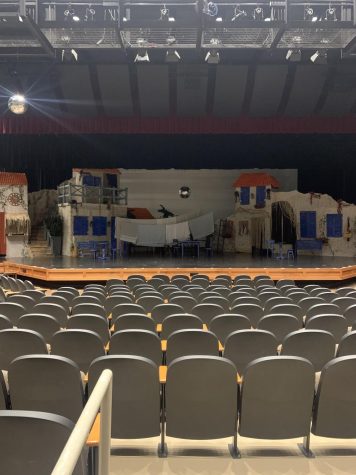
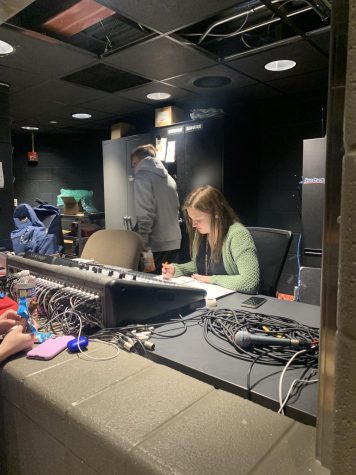
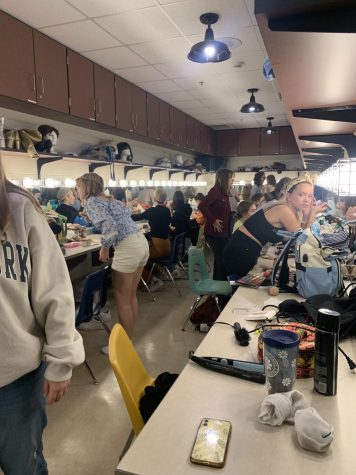
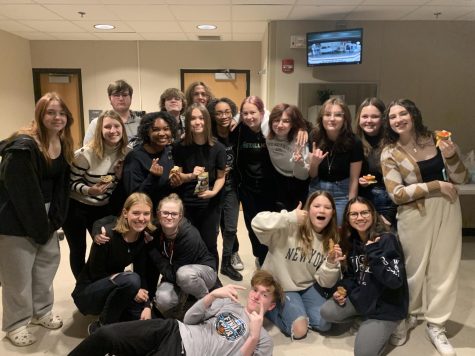
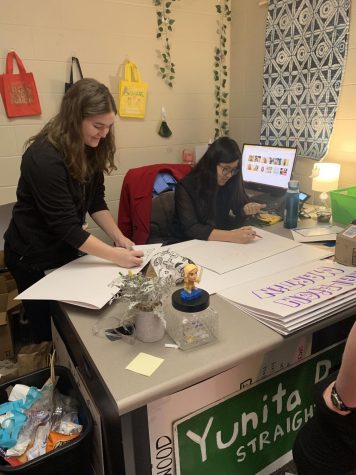
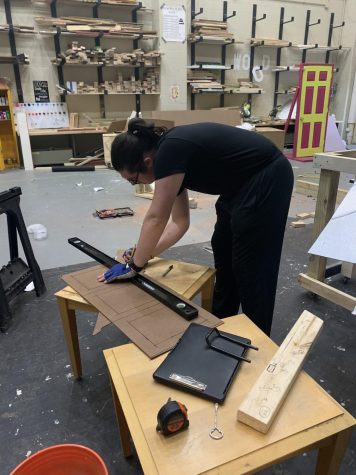
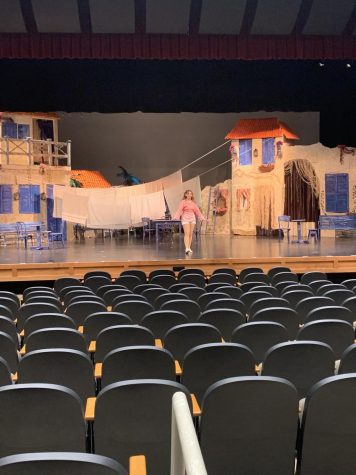
Working behind the scenes of Mamma Mia!, I found out just how much work goes into making such a production. It is truly a magnificent experience; only with the combination of set construction and painting, lighting, and sound, can a play work.
I spent most of my time working on set construction. My fellow construction workers started with either the dock or the bar. When those were finished, we moved them to the auditorium. We next needed to put ramps on both ends of the dock, so I worked on that task while some other people worked on the other buildings.
We ordered stair frames to put on the front of the dock, and we waited for weeks for them to arrive. Eventually, Ms. Nichols, the auditorium and tech director, checked the delivery status only to realize that they had arrived a week prior. They were sitting by the wrong garage door. After we finally brought them inside, one of them was found to be broken at one end. Luckily, we had to cut that entire portion off for it to fit on the dock.
After I cut the first one, I lined it up with the dock and jokingly said “Okay, guys. The stairs are finished.” One of my peers decided to try to walk up the unsecured stair frame, causing it to fall on my toe. It bled a little bit and is still bruised. Ms. Nichols gave me a frozen Uncrustables sandwich to act as an ice pack on my toe.
I next took a couple of weeks hiatus for fall break and to let my toe heal. When I got back, I was amazed by the progress that was made. At some point, the whole bar fell onto one of the construction members, so we had to lift it back to its proper position. The victim claimed and appeared to be fine.
The next large task on which I embarked was making pieces for the spiral staircase. I measured and cut each and every one of the verticals between the curved part of the spiral staircase. I was then told I had the wrong measurements, so I remeasured and recut all of the pieces. Once that was done, I was given my final large task, and I consider it my magnum opus.
My roofing quest began when Ms. Nichols asked me to make a roof that would fit onto a frame that was already made. I began by taking several measurements, so I could create an exact replica of the frame. The measurement and cutting of the pieces mostly involved a bunch of mathematics that are probably too boring to include, but I did a lot of it on a scrap piece of wood which I called my Calculation Board. It took me a few days to complete that roof, and I let my peers apply the first layer of paint, attach styrofoam cups, and repaint it to look like terracotta shingles. After that was completed, I was tasked with making two more roofs. Yay.
The first and third roofs had three sides, but the second roof was only able to have one side. It would be possible to give it a second side, but that would block one of the ramps onto the dock. Also, it had to be made of three pieces of material due to a lack of supplies. Great.
I ended up cutting the pieces for this second roof, and told people that it was ready for the process of painting and cupping. While I thought they were processing that roof, I made the frame on which it would stand. Little did I know, they did not realize that it was done, and the pieces were scattered all over the workshop. Lovely.
I knew I had to take a break from the roofing madness, so I worked on the railings for the spiral staircase. I made about half of them, and I had the persistence to make sure the ones I made were cut to fit perfectly. The person who made the other railings cut them close and wedged some thin scraps of wood to fill the gaps. Mine were the ones that do not have those wedges, although it is not easy to tell the difference. After that much needed mental health break, I got to work on the final roof.
At this point there was only a week left until opening night, so I was very stressed. I made sure to calm myself, because stress can cause crucial mistakes. The roof itself was made in an afternoon, and the painting, cupping, and repainting took the better half of a morning. After that was put up, the audio people needed help with running lines and songs, and those of us still there got to take part. There were snippets of our magnificent voices uploaded to the tech crew Instagram.
At the end of that day, I realized that somebody else in the tech crew wanted to have gift baskets to give to Ms. Nichols and Mr. Barber, the theatre directors. Of course, the baskets would be secret until we delivered them, but we decided to include pictures of cast and crew, stuffed animals, cards, and other kinds of small trinkets. I volunteered to make the picture frames, as a handmade gift is always better than a store bought one. Unfortunately, the frames didn’t fit the photographs, and we decided to use premade frames instead.
The week before opening night, we got into dress rehearsals. Some of the tech crew, including me, were designated to work as stage hands; a task that involves getting the set ready between scenes. The tech crew had to maintain absolute silence because almost every sound made can be heard in the audience. Unfortunately, some cast members got sick during rehearsals and unintentionally spread their illnesses to the crew. As soon as we found out, my little brother and I took covid tests. His came back positive, but mine were all negative. Instead, I caught the flu, and had to miss the final show.
Experiencing tech crew has helped me to get to know more people. It has solidified my belief that a good job can be done on a project, even if it is started at the last minute, and there often are several correct ways to get a job done. In general, I have made the tech crew my home, and hopefully I have not made anybody else sick.